马上注册,结交更多同行朋友,交流,分享,学习。
您需要 登录 才可以下载或查看,没有帐号?注册
x
本帖最后由 新锐 于 2014-6-13 18:08 编辑
现今塑料产品的制造,多材质射出成型(MCM)制程已经广泛地被应用于多元化的塑料件设计与制程。MCM制程主要是利用两种或多种材料,或使用相同的材料但不同的颜色,或是以回收材料和原料混合射出注入模具内来生产产品。利用此制程生产出的产品不仅融合了多种颜色,还可具备多种功能,比如皮层/核心层等三明治结构的组合。然而, 于现实生产中应用MCM制程,还是必须面临许多的问题与挑战。例如,MCM制程可能牵涉到多种嵌件、或多种不同材料,因此单一材料射出成型的设计与开发规则,常常不能直接套用于MCM。另外,由于MCM制程复杂性和多材质之物理机制,若以传统的单一材料射出成型的经验法则,很难推敲MCM制程与机理,因此无法有效对于关键成形条件进行优化或设计变更,造成质量控制上的不确定性。 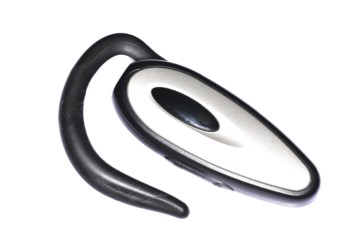
图一 具有多功能性的单一产品: (a) 多颜色材质化妆品包装瓶 (b) 模内装配而成的玩具 (c) 耳挂式耳机。 为了进一步厘清并了解MCM制程,以期未来能进一步掌握此等制程,首先,我们可以将非常复杂多元的MCM制程归纳成为两大类,如图二所示。第一类为当两种材料复合成型时,将产生明确之中间界面(distinct interface),此类常见的制程,包括嵌入成型(insert molding)、包覆成型(over molding)、和多射依序成型(sequential multiple shot molding)。第二类则为当两种材料复合成型时,将产生不确定之中间界面(uncertain interface),此类常见的制程,包括共射成型(co-injection),双射成型(bi-injection),针对不确定之中间界面系统,产品设计者如何能正确推测出最佳浇口位置,以及材料比例,使其成品得以获得理想的材料分布与产品特性,对产品设计人员将是相当大的挑战。
图二 多材质射出成型可分为两大类型: (左) 有明确之中间界面(distinct interface) ; (右) 不确定之中间界面(uncertain interface ) 因此,要解决MCM制程中复杂的特性与机理,并进一步加以掌握与控制,近年来大部份团队及成员都必须藉用CAE技术强大的模拟预测能力,以期能对潜在问题进行诊断分析并执行设计变更之事先验证。举例来说,小型触控式面板,当初原始设计是针对各别组件,一件一建分开射出,再组装而成。此方式产生组装后产品的翘曲问题虽少,但零组件间界面结合的强度可能受到影响,而且后段再组装也会是产品质量掌控之盲点。为此,利用MCM制程一体成形,透过包覆射出(Overmolding)成型(图三a所示),可以改善并提高对象界面结合的强度与后组装问题,但是制程中,由于两种不同的材料界面互相接触时,在后续冷却阶段将会产生区域积热现象 (图三b),导致产生严重的翘曲问题。由此可知,单件射出成型的产品设计与加工制程,不能直接套用在MCM产品制程中;而MCM制程所可能产生的翘曲问题,必须透过产品设计变更和不同的加工条件来解决。 图三 小触控式面板产品使用多材质射出成型制程: (a) 透过包覆射出制程(overmolding),产品发生严重翘曲问题 (b) 翘曲问题是由两种不同的材料界面互相接触时,所产生区域积热的现象所造成。 另一方面,共射成型(co-injection)制程中大多数皮层/核心层的结合可创造出许多新颖之产品,比如:产品可能为触感柔软的皮层/坚硬之核心层,或是纯料之皮层/回收料之核心层,或是纯料之皮层/含纤维强化之核心层等等的组合。若从实用面而言,共射成型制程普遍应用于汽车件、大众消费产品、和需要加强强度结构的产品制造上。进一步从开发内涵而言,此等制程必须面临主要的挑战是如何控制模具内的材料分布为理想状态。以耳挂式耳机产品为例(如图四所示),耳机挂钩设计必须连接手机和麦克风功能,与人体皮肤(耳朵)接触区域,该皮层材料必须具有良好柔软触感,但内在架构组成又必须具有足够的强度,避免产品变形。 a. | b. |
图四 耳挂式耳机: (a)几何设计 (b) 利用双射/共射制程,以PP材质为核心料和TPE材质为皮层料。 当此耳挂式耳机制作采用共射技术,以PP材质为核心料,以TPE材质当皮层料。理想上,应用共射成型制程可简化零件组装手续的崭新应用技术,并提供物料之间的接合界面具有更好的强度。然而,实际执行此类共射制程时,将面临许多挑战,例如:皮层料/核心层料之间的到底比例为何? 射出之相关条件要如何给定? 此时可事先透过CAE进行预测。 如图五所示,根据CAE模拟预测,使用50% 皮层料比例会导致核心层穿透皮层,造成产品质量瑕疵问题。再进一步执行皮层/核心层比例调适,可能70% 皮层料比例是较佳的选择。但是以此比例当基准,进一步预测产品变形问题时,我们发现产品具有严重翘曲问题,导致产品功能性不彰。 图五 利用共射制程开发制造耳挂式耳机: 50%皮层料比例,会导致较坚硬核心层料穿透皮层料,造成产品质量瑕疵问题。 接着,我们再利用CAE执行虚拟之设计变更,执行一系列之修改模具浇口位置设计验证,如图六所示;我们发现一些有趣且非常实务之解决方案,例如:应用图六(a) 所提之浇口方案,当采用40%之皮层料比例时,会导致核心层穿透皮层,原先思考这将会是造成产品质量瑕疵之严重问题;然而,应用CAE软件预测事先得知,使用40 %皮层料生产此对象,反而是最佳比例,因为较坚硬之核心料,在0.07秒时会穿透皮层,穿透现象发生后,该耳挂钩部结构件转换为仅使用较硬的PP材料,刚好提供更好的强度以符合产品强度要求。上述利用CAE技术事先预测,顺利解决产品制程与质量问题。
图六 利用CAE模流软件:帮助进行模具浇口位置优化验证。 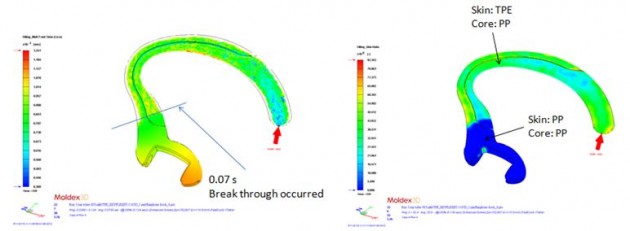
图七 (a) CAE软件成功帮助预测出使用40 %皮层料为生产此对象的最佳比例,此时较坚硬的核心层料穿透皮层料之现象会发生在0.07秒; (b) 穿透现象发生后,该耳挂钩部结构件转换为仅使用较硬的PP材料,来提供更好的强度以符合产品强度要求。 结论多材质射出成型(MCM)在现今的塑料产业中应用相当广泛。然而,由于MCM制程复杂性和多材料物理机制,以传统的单一射出成型的经验法则来推敲MCM制程,将遭遇许多困难,无法有效提供关键成形条件进行优化或设计变更,造成产品质量瑕疵问题。然而透过CAE模拟分析技术,不论是包覆射出成型(Overmolding)或是共射成型(co-injection molding),都可提供有效的产品设计验证、浇口位置优化,最大可行的核心层料比例预测(包括预测是否会发生核心层料穿透皮层料的现象),并考虑材料之间的相互作用影响,成功预测产品收缩和翘曲率来改善的产品质量的利器。 参考文献
1. US patent #3,051,994.
2. Multi-material Technology, Battenfeld.
3. Web source https://www.engelmachinery.com4. Chao-Tsai Huang et al, SPE ANTEC, 1888-1892 (2006).
5. P.J. Garner and D.F. Oxley, British Patent 1,156,217 (1971).
6. V. Goodship and J.C. Love, Multi-Material Injection Molding (2002).
7. R. Seldén, Polymer Engineering & Science, 40, 1165 (2000).
8. F. Ilinca, J.F. Hetu, and A. Derdouri, International Journal for Numerical Methods in Fluids, 50, 1445 (2006).
该贴已经同步到 新锐的微博 |