马上注册,结交更多同行朋友,交流,分享,学习。
您需要 登录 才可以下载或查看,没有帐号?注册
x
3D打印和快速成型在制造业早已时有所闻,随着3D打印机的价格越来越平易近人,自产自制已非遥不可及。然而,对于大多数的产品而言,模具仍有其存在的必要。快速成型的概念应用在制造异型水路已有二十余年,透过雷射烧结能够依照产品表面轮廓,制造出任意形状的冷却水路,藉此缩短成型周期并创造质量更高的产品。 异型水路制造挑战除了雷射烧结外,还有其他方法可以制造异型水路,像是真空铜杆和数控加工技术,其中又以雷射烧结的设计灵活性最高,不过价格也是最高。雷射烧结也存在一些缺点,例如模具板会因为雷射二极管的高能量而产生偏移。另外,过度粗糙的管道表面则容易导致水堵塞。其他挑战像是烧结尺寸和材料限制,都已获得极大的改善,使得雷射烧结更适用于制造异型水路。 产品缺陷藉由改变冷却设计,让水路更贴近产品轮廓,温度分布将因此变得更均匀且能消除冷热点,减少产品因热产生的缺陷,如:残余应力、翘曲、气孔和凹痕等问题。 产品缺陷通常与产品本身设计相关。举例来说,如果一个产品有设计肋条,肋条的反面往往会出现凹痕;如果冷却速率太快,则很有可能会出现气孔。尽管产品缺陷的原因很多且十分复杂,但如果设计得当,异型水路仍然能够有效改善产品翘曲情形。我们接下来将会检视异型水路如何解决常见的凹痕和翘曲问题。 使用异型水路的必要性异型水路有许多广为人知的优点,但由于异型水路成本较高因此在业界并不普及。一个最常见的问题是:我真的需要用到异型水路吗?这是一个关乎投资到酬率的问题。一般来说,杯型/盒型产品和曲率变化大的产品最适合使用异型水路。另一个重要的考虑是产品厚度,由于塑料是热的不良导体,如果产品太厚,即使成功缩短成型周期也可能无法补贴烧结所需的成本。 此外,异型水路究竟能改善多少翘曲?又要如何在建模之前得知呢?利用CAE软件进行仿真将可以获得解答,而以下两个案例将可以充分展现CAE软件在模具设计初期所带来的价值。 凹痕问题第一个案例是一个平均厚度为三厘米的电钻盖子,产品的轮廓十分适合使用异型水路。如图一与图二所示,如果冷却时间不足,红色圈起来的地方会产生凹痕。为了要免除中间的凹痕,图三的隔板式水路设计需要花费三十秒,但如果使用异型水路,只需二十秒即可抑制凹痕出现(见图四) 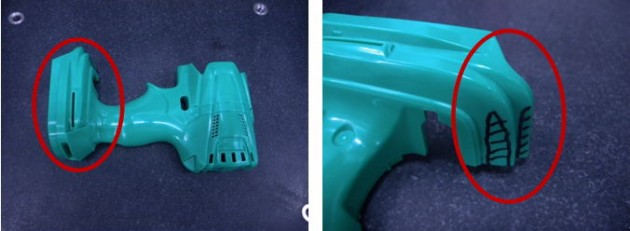
图一和图二 红色圈指出电钻产品发生凹痕处
透过模拟,将可以很轻易凸显异型水路的成效。在一致的温度范围下,图五是隔板式水路设计(左)与异型水路设计(右) 的温度分布比较图。在使用异型水路之后,产品核心处的温度即比传统隔板式水路来得低。仿真结果显示的最大凹痕位置(见图六)也与实际成型的结果一致。 | | 图五 隔板式水路设计(左)与异型水路设计(右) 的温度分布比较图 |
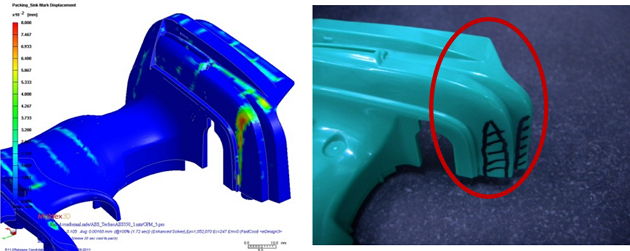
图六 Moldex3D凹痕位置仿真结果与实际成型的结果一致 翘曲问题第二个案例是一个数字相机的盖子(见图七),如果只在核心处使用隔板式水路(见图8)将会发生严重翘曲问题。透过异型水路(见图九),翘曲现象获得明显改善 (见图十)。在此案例中,异型水路不仅能改善翘曲问题,冷却时间也缩短近百分之三十(从十三秒减为九秒)。 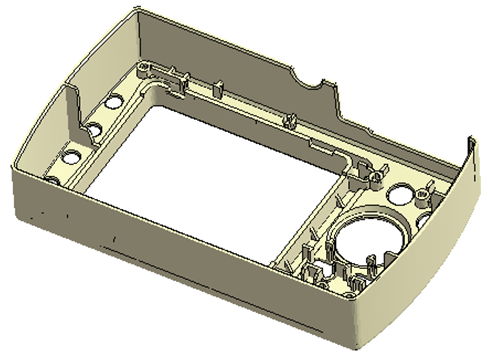
图七 数字相机外壳盖
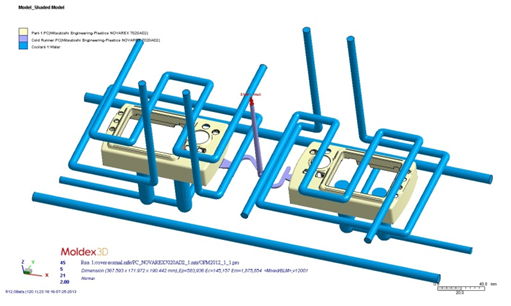
图八 传统隔板式水路
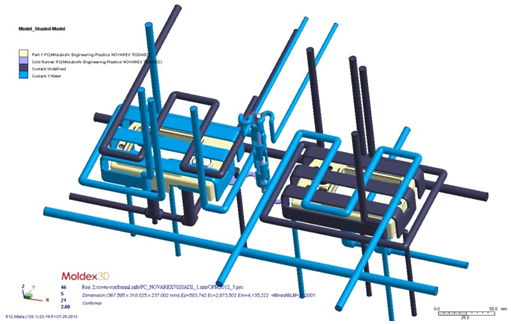
图九 异型水路
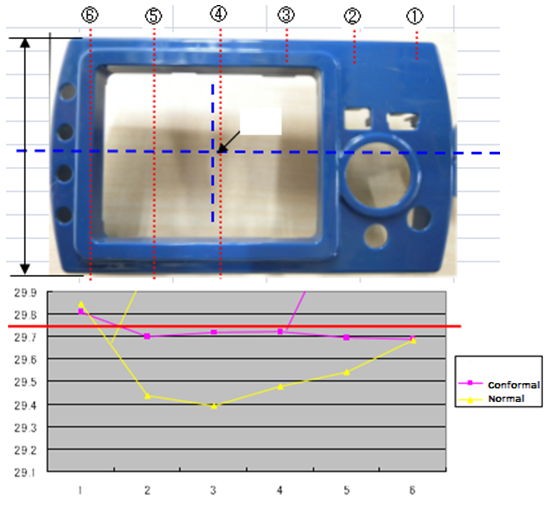
图十 翘曲值获得明显改善 总结异型水路主要是使用雷射烧结技术进行生产制造,主要有优势为:(一) 缩短成型周期 (二)提升产品质量。为了能更精准掌握异型水路的投资报酬率,必须藉由科学工具协助。经由以上两个案例可得知异型水路在改善凹痕、翘曲和成型周期都有显着的成效,而CAE软件则可以有效地仿真这些优点。 特别感谢非常感谢OPM公司提供这些案例分享以及详细的实验数据,才得以促成这项验证研究。
该贴已经同步到 新锐的微博 |